When it comes to marine applications, selecting the appropriate wire rope is crucial for ensuring safety, durability, and reliability. Galvanized wire rope is a popular choice due to its resistance to corrosion and ability to withstand harsh marine environments. However, choosing the right marine galvanized steel wire rope involves considering several key factors. In this guide, we will explore the essential aspects to keep in mind when selecting marine galvanized wire rope.
Galvanized Wire Rope For Marine Applications
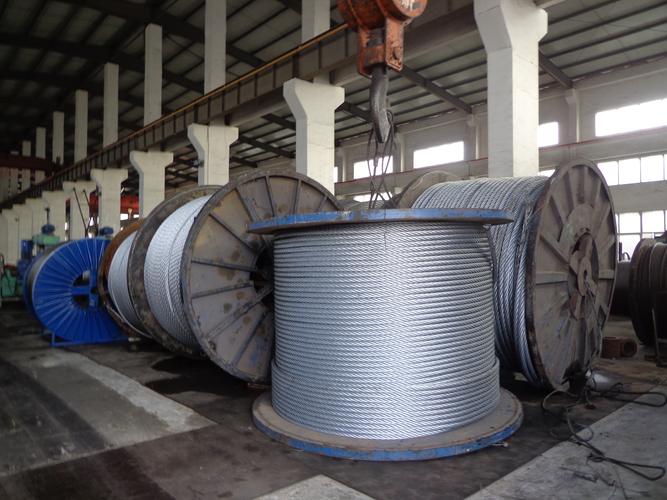
Galvanized wire rope is made by coating regular steel wire with a layer of zinc. This galvanized coating provides excellent corrosion resistance, making it ideal for marine applications where exposure to saltwater and moisture is common. The thickness of the galvanized coating can vary, influencing the rope’s durability and lifespan.
Coating Types Of Galvanized Steel Wire Rope
Marine galvanized steel wire ropes can have different types of coatings, each offering specific benefits. Common coating types include:
Hot-Dip Galvanized
In this process, the wire rope is immersed in a bath of molten zinc, providing a thick and durable coating that offers excellent corrosion protection in marine environments.
Electro-Galvanized
This method involves applying a thinner layer of zinc to the wire rope through electrolysis. While not as robust as hot-dip galvanizing, electro-galvanized ropes are more cost-effective and suitable for less demanding marine applications
Zinc-Aluminum Coating
Some wire ropes feature a coating of zinc-aluminum alloy, offering enhanced corrosion resistance compared to pure zinc coatings. These ropes are well-suited for marine applications that require superior durability.
Powder Coating
Wire ropes also can be coated with a layer of powder for additional protection against corrosion and abrasion. Powder-coated marine galvanized steel wire ropes are ideal for applications where aesthetics and color customization are important.
Galvanized Wire Rope Construction
Marine galvanized wire ropes come in various constructions, each designed for specific applications.
1x19 Wire Rope
This configuration consists of one central strand surrounded by 19 smaller strands. 1×19 wire ropes offer high tensile strength and minimal flexibility, making them ideal for applications where strength is paramount, such as standing rigging on sailboats.
7x7 Wire Rope
In a 7×7 construction, the marine wire rope is made up of seven main strands, each composed of seven smaller wires. 7×7 wire ropes are more flexible than 1×19 ropes, making them suitable for applications like cable railing and general-purpose marine use.
7x19 Wire Rope
This construction features seven main strands, with each strand consisting of 19 smaller wires. 7×19 marine wire ropes offer a balance between strength and flexibility, making them versatile for various marine applications, including lifting and rigging purposes.
6x19 Seale Construction
The 6×19 Seale configuration features six main strands, each with multiple smaller wires. This construction provides good flexibility and fatigue resistance, making it suitable for dynamic lifting applications in marine environments.
Rotation-Resistant Construction
Some marine wire ropes are designed with special constructions to minimize twisting and rotation under load. These rotation-resistant marine wire ropes are essential for applications where stability and control are crucial, such as crane operations on ships.
Galvanized Wire Rope Choosing Considerations
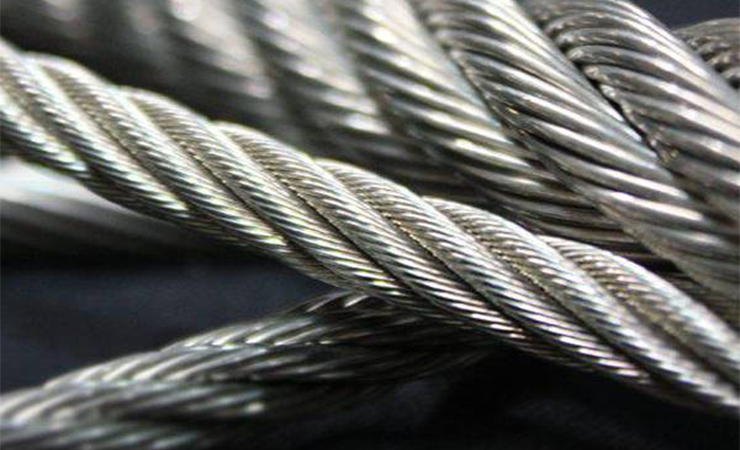
When choosing the right galvanized wire rope for marine applications, several key considerations should be taken into account to ensure optimal performance and durability. Here is a list of important factors to consider:
Application Requirements: Understand the specific purpose of the wire rope in your marine application, whether it’s for lifting, rigging, anchoring, or other functions.
Working Load Limit (WLL): Determine the maximum load that the wire rope will be subjected to during operation to ensure it can safely support the intended loads.
Breaking Strength: Consider the wire rope’s breaking strength, which is the maximum load it can withstand before failure. Ensure the breaking strength exceeds the maximum expected loads.
Construction Type: Choose the appropriate construction (e.g., 1×19, 7×7, 7×19) based on factors like strength, flexibility, and suitability for the application.
Coating Type: Decide on the type of coating (e.g., hot-dip galvanized, electro-galvanized, zinc-aluminum coating) based on the level of corrosion resistance required for the application.
Environmental Conditions: Consider the specific marine environment where the wire rope will be used, including exposure to saltwater, UV radiation, temperature variations, and other factors that may affect performance.
Recommended Galvanized Wire Rope For Different Marine Applications

When selecting galvanized wire rope for marine applications, it’s essential to consider the specific requirements of the intended use. Different coatings and constructions offer varying levels of durability, flexibility, and corrosion resistance.
Standing Rigging on Sailboats
- Recommended Construction: 1×19
- Recommended Coating: Hot-Dip Galvanized
- Reasoning: 1×19 construction provides high tensile strength, suitable for standing rigging. Hot-dip galvanizing offers robust corrosion protection against saltwater exposure.
Lifting and Rigging on Marine Vessels
- Recommended Construction: 7×19
- Recommended Coating: Zinc-Aluminum Coating
- Reasoning: 7×19 construction balances strength and flexibility, ideal for lifting and rigging applications. Zinc-aluminum coating provides enhanced corrosion resistance in marine environments.
Cable Railing Systems
- Recommended Construction: 7×7
- Recommended Coating: Electro-Galvanized
- Reasoning: 7×7 construction offers flexibility for cable railing systems. Electro-galvanized coating is cost-effective and suitable for less demanding marine applications.
Crane Operations on Ships
- Recommended Construction: Rotation-Resistant
- Recommended Coating: Hot-Dip Galvanized
- Reasoning: Rotation-resistant construction minimizes twisting during crane operations. Hot-dip galvanizing ensures durability and corrosion protection in harsh marine conditions.
Dynamic Lifting Applications
- Recommended Construction: 6×19 Seale
- Recommended Coating: Powder Coating
- Reasoning: 6×19 Seale construction provides flexibility and fatigue resistance for dynamic lifting. Powder coating offers additional protection against corrosion and abrasion.